Expert Insight
Industry 4.0:
Seize the Moment (in Small Steps)
Manufacturing has remerged as a growth area in the West, and particularly in the UK, fuelled by innovative new technologies that combine to form Industry 4.0. But a lack of knowledge is limiting organisations’ ability to embrace the opportunities. Siert Wijnia, co-founder and CTO of Ultimaker, explains how organisations can leverage 3D printing to maximise the potential of the light bulb moment
The UK government’s sudden interest in and commitment to the manufacturing sector may have taken companies by surprise, but the investment is timely: manufacturing processes are being transformed at a speed unseen since the last industrial revolution.
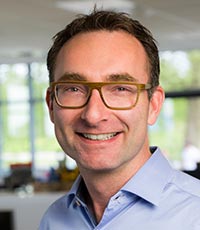
Siert Wijnia, co-founder and CTO of Ultimaker
But with so much excitement surrounding Industry 4.0, are organisations at risk of becoming bogged down in strategising and conceptualising, rather than grasping the opportunity? A lack of knowledge combined with often low digital confidence is challenging innovation – especially given the potential step change in operations required to embrace robotics and AI on the production line. It is, therefore, important to take a step back: put the AI robots to one side, and understand what is achievable today.
Industry 4.0 is, essentially, all about digitisation. It is about leveraging connected technologies to streamline processes and achieve not only new levels of efficiency but also new manufacturing models that transform the ‘idea to prototype to production’ cycle; that capture that light bulb moment of genius. And that is where increasingly accessible – and cost effective – technologies such as 3D printing are fast coming to the fore, especially within prototyping.
Collaborative prototyping: the potential of 3D printing for Industry 4.0
UK manufacturing has come under the spotlight in recent weeks. While the industry can point to record order books, companies are being lambasted for a lack of investment and an over-reliance on a favourable exchange rate and cheap labour when compared to European competitors.
The head of Siemens UK recently called on UK companies to prepare for the fourth industrial revolution, (also known as Industry 4.0) led by AI, 3D printing and robotics, citing a report that says the technologies could boost manufacturing in the UK by £445bn and create 175,000 jobs over the next decade.
And while the government now appears committed to increasing its investment in the sector, the new technologies, from AI to Robotics, can appear daunting. Given the innovation occurring globally, however, organisations need to start considering the implications of this next industrial revolution – but in small steps, not business risking technological upheaval.
Rather than look to revamp the entire production line, just consider the way individuals and companies can collaborate on new ideas when prototype files are shipped around the world and then 3D printed on demand, rather than waiting days, even weeks, for a physical product to arrive.
“With the price point of each iteration significantly reduced by the use of low-cost 3D printing, organisations can be far more confident about pushing for multiple iterations to fine tune the concept”
Firstly, individuals retain the momentum; with no delay in the process, the physical and mental connection to the new concept or idea is retained. Secondly, with the price point of each iteration significantly reduced by the use of low-cost 3D printing, organisations can be far more confident about pushing for multiple iterations to fine tune the concept.
Prototypes can be tried more quickly, even in parallel, maximising the knowledge of the collaborative team to quickly and effectively green or red light the concept. Essentially, the business has a chance to grab that light bulb moment and bring it to realisation faster than ever before.
In addition, the use of 3D printing makes it far easier to gain feedback and useful response from potential users – individuals who may either struggle to visualise product pros and cons when presented with an on-screen diagram, or indeed those who don’t have access to the tools they have to work with.
Providing orthopedic surgeons, for example, with the ability to create a 3D model of a bone they need to operate on to facilitate the planning of complex surgeries brings numerous benefits, including significant reduction of surgical costs and better patient education.
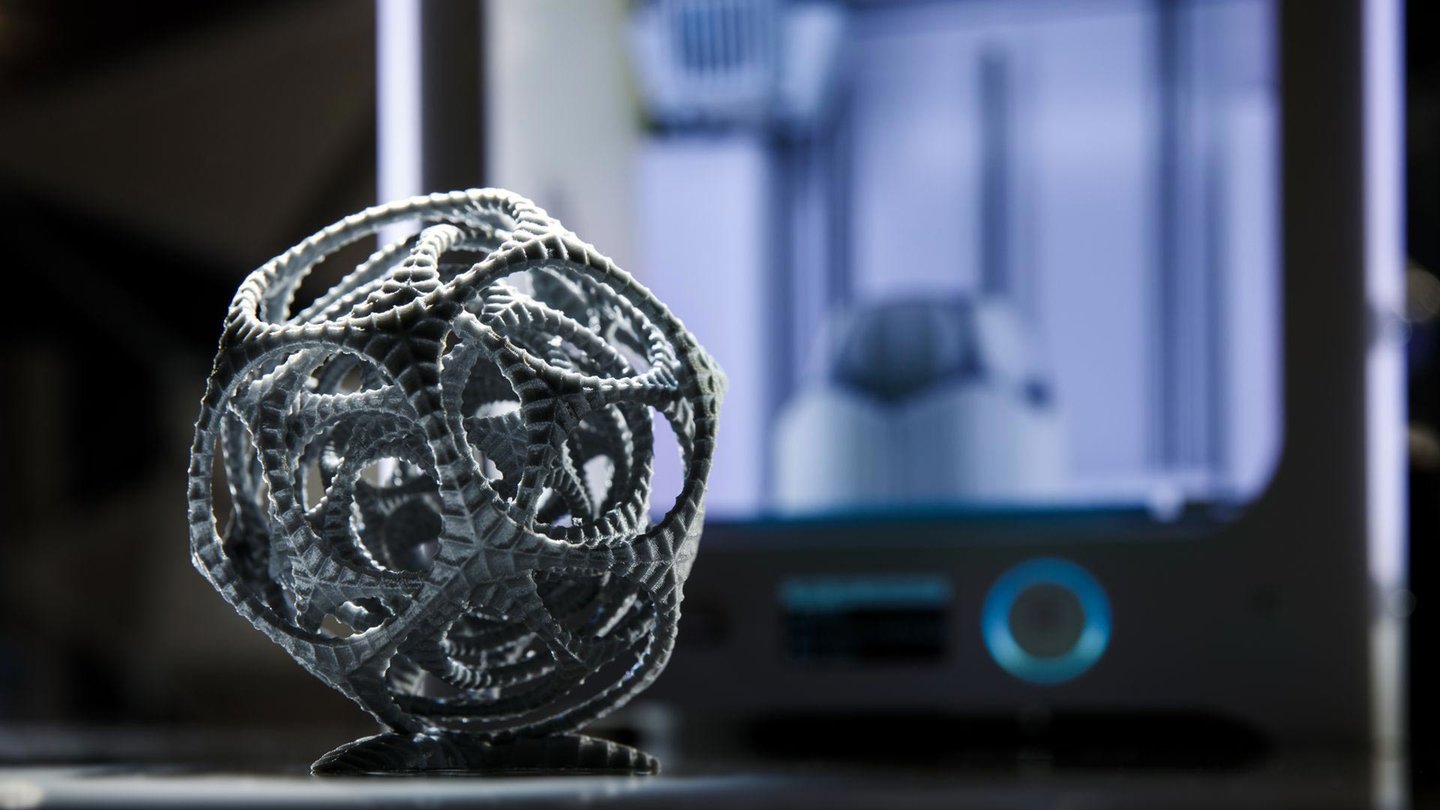
Innovation in practice: how rapid prototyping can transform business processes
The entire prototyping process can be reconsidered, enabling new business processes, even opening up new markets. For example, with the cost of 3D printers there is now no need for organisations to outsource prototype creation as many have in the past.
Rather than spending hundreds, even thousands of pounds on a prototype, it can be created in house for just tens of pounds – including the cost of printer depreciation. The economics are fundamentally different.
Indeed, new companies are springing up producing not for the masses but creating specialist products that have a production run in just the hundreds – using 3D printing only to cost effectively meet the demands of a specific niche market.
Price is, in fact, a very small component of the overall benefit; it is the way organisations can bring new ideas to market that is truly compelling.
“Without techniques like machine learning we couldn’t recommend products other users have bought but we will be able to do that with our technology later this year”
For example, one firm is using 3D printing to test new ideas for internal parts and mechanisms. Experimenting with multiple iterations is speeding up the process of refinement and making it easier for the company to take the tough ‘go to market’ decisions. From the initial spark of an idea to a 3D printed model can take a matter of hours – it can be tested, tweaked, and tested again, all based on an accurate representation of the final product or part.
The process can also be used to confirm a product’s manufacturability without needing to invest in expensive tooling. Traditionally, design engineers have been unable to fully test the functionality of designs without expensive and often time consuming changes to the manufacturing process – changes that have to be repeated each time a design modification is introduced.
Integrated 3D printing solutions fundamentally change this process – enabling organisations to confidently offer customers a chance to rejig designs without incurring an untenable cost. The result is a more flexible, interactive customer relationship as well as faster and lower cost time to market.
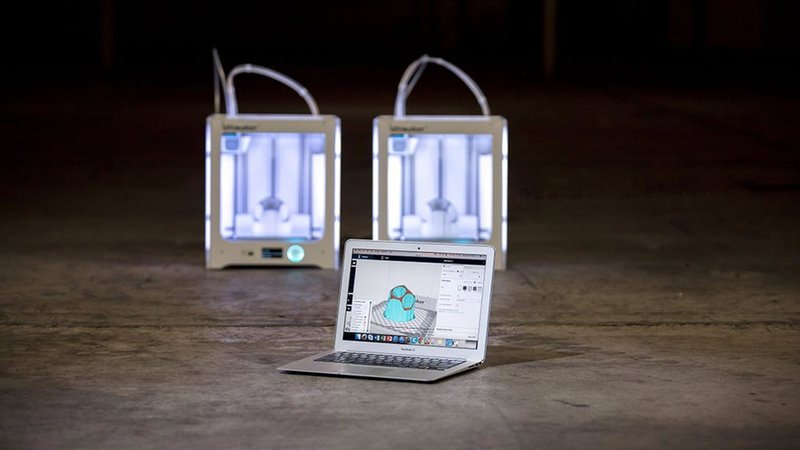
Grasp the moment: innovating in short time frames
One of the most compelling aspects of this prototyping model is its accessibility – in a world of disruptive technology, 3D printing can be embraced without affecting any aspect of the traditional manufacturing production line. Organisations can take a small, but significant, step towards digitisation and Industry 4.0 without a massive investment and without the huge and potentially risky upheaval associated with AI robotics.
And this is key: Industry 4.0 is about streamlining manufacturing and 3D printing has a significant role to play in this process. It is an accessible and affordable way of better streamlining the production life cycle - from concept to manufacturing.
Moreover, it is enabling inspired individuals to grasp the moment – to leverage digitisation and transformative technologies to turn a fantastic idea into a viable product within an incredibly short time frame, strengthening the concepts that underpin Industry 4.0.
“When a young engineer can create a functional prototype in a couple of hours, a new product idea can be realised during the time it takes to run an Industry 4.0 strategy meeting”
Plus, while AI robotics remains theoretical, with new graduates emerging from university familiar with 3D printing technology and its application, companies have fast access to the skills required.
With the renewed government commitment to UK manufacturing it is time to seize the moment. Organisations cannot rely on favourable exchange rates to boost the order books forever – especially as the rest of the world fervently embraces Industry 4.0.
But in the rush to get involved it is important to avoid over-strategising. Don’t get lost in ‘what Industry 4.0 should mean for the business’ task forces.
When a young engineer can create a functional prototype in a couple of hours, a new product idea can be realised during the time it takes to run an Industry 4.0 strategy meeting. That, surely, provides the business case for taking the first step towards a totally digitised and connected manufacturing environment.
Images courtesy of Ultimaker